A semicircular chisel is more popular with the carver than a straight chisel, especially in the width of a little finger. Practically it is enough to have four or five semicircular chisels of different radius of curvature and width of blade, i.e. sloping, medium, steep.
Two small chisels can be successfully made by yourself from round files: one 6 mm in diameter, the other 9 mm. This work is more delicate than with straight chisels, but it gives the cutter a very handy tool.
For this purpose, a round file of a fine notch is annealed (heated reddish, for example on a gas torch, and given free to cool) and other round file or nadfil, depending on diameter of the cutter, select a valley groove as much as possible at a sharper angle to an axis of the cutter. Three pictures of such a pick are given; the local section shows the angle of the file when selecting the fractional groove. The work is done with the pick clamped in a vise.
The process of groove selection will be less labor-consuming, if preliminary the file is bent in a hot condition at the angle allowing to select a groove only on the final part of the pick, and then, after final processing, it is straightened again, also in a hot condition.
When the groove is selected up to the formation of a sharp edge on the end of the pick, this edge is sharpened at a small angle from the outer side on the bar, constantly turning the cutter to completely bring in the corners. A sharp edge is also formed on the sides of the pick. With such a cutter it will be convenient not only to pick out wood, to make semicircular grooves, but also to drill hollows and even small holes by turning the cutter to the left and to the right.
Grinding and polishing both inner (face) and outer surface (chamfer) is done on emery paper: firstly, a nadfill is cleaned and then the inner cylindrical surface is polished to a shine by moving the cutter along a metal rod of corresponding diameter (for instance, the smooth part of the drill) clamped in a vice and wrapped with fine emery paper. The wiped paper is replaced with new paper.
Next, a chamfer is polished on the dressing board while simultaneously sharpening the cutter blade. This is done with rapid, transverse movements in the direction of the cutter axis, and the cutter is constantly rotated. The burr that develops is removed from the inside with a paper rod as described above. The cutting edge is brought to working condition and only then the cutter is hardened.
Further on in the process of carving, it is convenient to adjust the cutter from the concave side on the handle of a painting brush, on which a strip of sandpaper is placed on top. The conical surface of the brush handle allows you to take the appropriate diameter depending on the curvature of the carving notch. The cutter is placed by the surface of the whole groove on the handle of the brush with paper and is pulled toward you, the emphasis is placed on the cutting edge. A burr appears on the convex side of the blade, which is immediately removed by dressing the convex surface of the cutter on the dressing board. The burr is bent inward again, then the operation is repeated on the brush handle, etc. – with more and more frequent changes in the dressing of both sides of the pick until the burr disappears.
It is advisable to buy semi-circular chisels (large diameters in the senesia) in a store, changing only by cold sharpening the chamfer angle to sharper (as in straight chisels) and rounding the corners, if the chisel is not intended for geometric carving. It is possible to remove the corners of the blade of such a chisel, and significantly, giving it the shape of a chisel, then the chisel will be convenient for roughing out wood or for working on a lathe.
If necessary, a carver can make a semicircular chisel by himself according to the method of making the above described cutters. The following workpieces are used as blanks: semi-circular or triangular file, chisel, any quality steel rod of corresponding cross-section. The annealed workpiece is rounded on the outside to the shape of the chisel profile. In the hot state is bent her end (length 6 – 8 cm) for convenience, a sample of internal grooves and performed. all the above described operations for the manufacture of cutters.
Of course, the work will be simplified if the master will have a tube (better yet – half a tube) of good steel. Then it can be processed cold. This guarantees success, as the risk of the most capricious operation – hardening – is eliminated.
If you have the two cutters described above, it is necessary to have at least one semicircular chisel with a blade width of 15 mm.
It is possible to make a semicircular chisel by cold method from the usual straight chisel bought in a store, having chosen on its end by an angle of an abrasive sharpener a groove-shaped notch and having rounded in the other side. Then remove the chamfer forming the blade and sharpen it. The difficulty in this case is the need to be careful when working on the sharpener with large revolutions, so as not to burn the end of the chisel, constantly dipping it in water and watching for boiling water droplets on the surface.- The second difficulty is to align and sharpen the groove. It depends on the means at the master’s disposal: a small grinding wheel with a sharpened disk rim; a small bar rounded to the chisel shape on the same sharpener; a metal rod wrapped in sandpaper, etc.
It is clear that if a craftsman is familiar with heat treatment of steel and has the ability to harden the tool, then the manufacturing operations are simplified.
When sharpening and dressing semi-circular chisels, the outer surface of the cutting edge (chamfer) is first machined on a block, then on an arbor or dressing board. The movements of the chisel are reciprocating at a 45° angle to the direction of the chisel rod, while the hand of the right hand is constantly turning, so that not only the chamfer is treated, but also the corners of the blade are rounded (as mentioned above).
Note that sharp corners of chisels interfere with the work, leave scratches, cuts, i.e. reduce the maneuverability of the tool and the cutter. As a rule, a semi-circular chisel is a universal tool, which is used to process not only concave, but also convex surfaces (the shape of grapes, for example, and of different curvature). In this case, achieving a change in the curvature of the convex surface with the appropriate clone chisel, the cutter will face the fact that the sharp corners of the blade will cut into the work surface, leaving traces on it.
Rectangular corners of the blade in straight semi-circular chisels (and making strictly right angles on the blade of chisels is recommended in almost all literature) are necessary only to perform certain, as a rule, repetitive operations according to a given pattern, which is most often found in carving, where a strict geometric pattern of the ornament is sustained.
Obviously, the question of the shape of the chisel blade should, subject to the remarks, be left to the carver’s discretion – it depends on the nature of his carving. It is better, of course, to have both in a set.
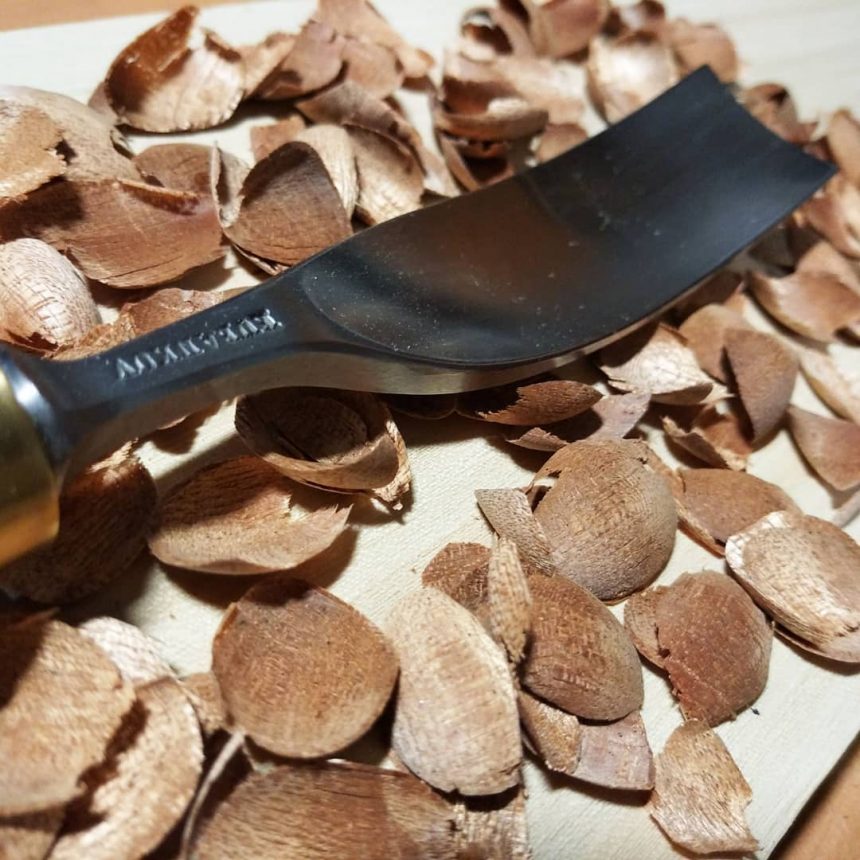